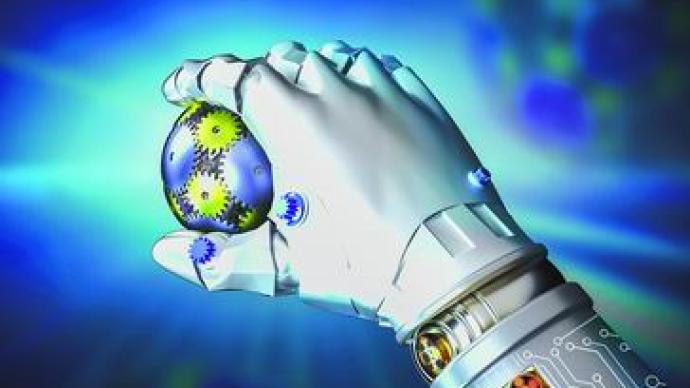
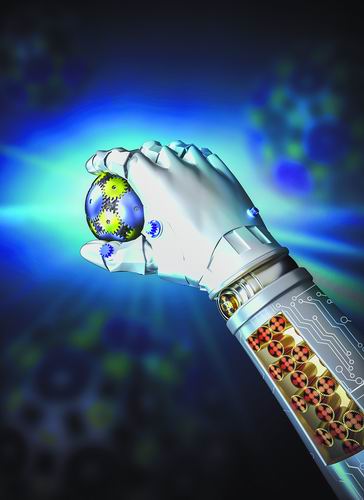
The reporter learned from the National Defense University of Science and Technology on September 12 that researchers at the school proposed an original intelligent metamaterial design method, which realized a large-scale, continuous and rapid adjustment of the stiffness and shape of metal-based materials, which is of great scientific importance. Significance and engineering application value.
The related research was recently published in "Nature-Materials" as the cover article in August, and was rated as an important global scientific and technological progress in June this year by "Nature" (a total of 4 items in the world).
Gear cluster enables mechanical performance adjustment
In recent years, smart materials have attracted a lot of attention, and they are the basis for smart equipment and structural design. The adjustment of material elasticity is necessary for intelligent machines, robots, airplanes and other systems. However, once the conventional materials are prepared, their properties can hardly be changed, and some materials can only exhibit a certain degree of adjustment during high temperature phase transition, but they do not have practical engineering operability.
"Mechanical/mechanical metamaterials are structural and functional materials with mechanical properties beyond conventional materials, providing cutting-edge technical support for high-performance equipment design, but traditional metamaterial design methods still cannot achieve stable and continuous parameter control, requiring disruptive design thinking skills. Break through this bottleneck." said Wen Jihong, the leader of the vibration and noise control research team at the School of Intelligent Science of the school and the co-corresponding author of the paper.
"The fundamental reason that restricts the realization of intelligent adjustment of mechanical metamaterials is that the design of traditional metamaterials follows the same pattern, that is, single-function load-bearing primitives such as beams, rods, and plates are connected with fixed or buckling nodes to form a deterministic topology structure. In this mode, when stimulated by stress, heat, or electromagnetic fields, the metamaterial will reconfigure due to buckling or rotating hinges, thereby changing stiffness, while causing plastic deformation and discontinuous changes, making the adjustment process very difficult." Fang Xin, the first author and co-corresponding author and an associate researcher of the research team, said.
To solve this problem, the research team proposed an intelligent programmable mechanical/mechanical metamaterial design paradigm based on multifunctional dynamic primitives and variable-firm coupling modes, and designed a series of gear-based intelligent metamaterials, breaking through the macro and micro, The integrated integrated manufacturing and integrated driving technology of metal-based and composite-based metamaterials realizes large-scale, continuous, and rapid adjustment of metal-based materials.
In layman's terms, the team designed a smart material made of gears that can make solid materials harder/softer or deformed as the gears rotate, according to different "commands."
"This is an unprecedented design method." Fang Xin said the tunability can be achieved by assembling components with built-in stiffness gradients. To achieve mechanically tunable yet robust solids, it is necessary to ensure tunability and strong coupling (reliable connection) under large forces, while avoiding plastic deformation during adjustment. "We found that this variable yet strong coupling can be achieved through clusters of gears."
Fang Xin revealed that in addition to trying to use gears as primitives, the team also tried many other configurations, such as the widely concerned origami configuration, various elastic buckling configurations, bistable/multi-stable configurations, but none of them could achieve the regulatory properties they want.
Why a gear cluster? "Reliable gear meshing can smoothly transmit rotation and heavy compressive loads." Fang Xin said that stiffness gradients can be built into individual gear bodies or achieved through layered gear assemblies. Gear sets can be assembled into groups of cells, and the cells, when properly arranged, can form metamaterials.
Get inspiration for internal structure design from Tai Chi diagram
Since the gear is a usable element, how should its internal structure be designed?
The tunability of metamaterials depends on the shape of their built-in hollows. "To achieve tunable but strong materials, it is necessary to ensure tunability and robust controllability under large forces, while avoiding plastic deformation during tuning." Fang Xin said that among many design schemes, the team started from Tai Chi. Taking inspiration from the picture, we finally designed a gear shaped like a tai chi diagram, whose shape is characterized by the direction of the spiral, which can provide smooth changes and polarities.
"The inspiration for Tai Chi map was obtained from traditional Chinese culture. At that time, I was thinking of various simple, atmospheric and useful shapes with a pen, and suddenly the "Book of Changes" in "two yi generates four images, and four images generate gossip" suddenly flashed in my mind. This sentence reminds me of Tai Chi diagram. Because the core idea of Tai Chi is 'change', and the material properties we want are also 'change'." Fang Xin said, "After introducing the concept of Tai Chi, the configuration we designed Having positive and negative polarities provides a nice design dimension."
On this basis, the team used tightly coupled periodic gears and two lattice frames (front and rear) to arrange the gears in a simple pattern, with two elastic arms formed on the outside, whose radial thickness varies smoothly with the rotation angle θ. Under the action of compressive load, the deformation of the arm is mainly bending.
"The rotation directions of any two meshing gears are opposite. The helical directions of the front and back Tai Chi patterns are opposite. Therefore, the meshing pattern of a pair of gears has two poles. When the helical directions of the patterns are opposite, the polarity is positive, On the contrary, it has negative polarity." Fang Xin said.
To test this idea, the team fabricated an integrated miniature metamaterial consisting of 5 rows and 6 columns of Taiji gears using projection microscopic stereolithography 3D printing technology. The diameter and tooth thickness of Taiji gears are 3.6 mm and 235 microns, respectively, and the thickest arm is 75 microns. The samples were made of photosensitive resin with a Young's modulus of 3.5 GPa.
"The equivalent modulus Ey (θ) of this miniature specimen can be adjusted smoothly by 35 times (from 8.3MPa to 295MPa). The adjustment range of samples prepared with metal materials can reach 75 times." Fang Xin said, this means Therefore, even at the microscale, gear-based integrated metamaterials can be directly fabricated by 3D printing. The main challenge in this integrated manufacturing is to ensure that the meshing teeth do not fuse together, but still participate effectively in meshing.
Rotate the transmission planetary gear to "transform"
The first metamaterial designed by the team is only tunable under compressive loads. "We expect to find a design method that can tune both the compressive and tensile moduli while maintaining structural integrity." Fang Xin said, the team explored and found that this can be achieved by organizing the planetary gear system into cells accomplish. Using clusters of planetary gears, the team created a layered metamaterial whose tunability comes from the relative rotation of the gears within the cell.
"The variable stiffness of the planetary gear metamaterial we designed comes from the inside of each planetary gear. The gear ring produces elastic bending deformation, and the inner planetary gear is the fulcrum of the deformation of the ring gear, and it can be changed by changing the position of the gear ring by rotating the planetary gear. For the assembled metamaterial, all the sun gears are connected by shafts to the gears that transmit the rotation, and these transmission gears are tightly coupled together, Fang Xin said. Therefore, all elements can be reconfigured and adjusted by simply turning a few of the transmission gears.
"Interestingly, the metamaterials we designed are stable under large compressive forces and exhibit large stiffness in shear. One of the factors supporting the stability is a self-locking mechanism of the gear set, Another factor is the bite force of the gear teeth." Fang Xin said.
The team proposed several scenarios that could demonstrate the broad potential of gear-based metamaterials. “For robots, adjustable stiffness legs/actuators can provide high stiffness to support heavy loads stably while walking, and low stiffness to provide shock-absorbing protection when jumping or running. Similar adjustable stiffness isolation is required in aero-engine pylon systems to maintain the best performance and efficiency in different flight phases," said Wen Jihong.
"One can also envision 3D metamaterials by using bevel gears, assembling flat gears into layered structures, or synthesizing different types of gears, using integrated manufacturing to connect these tunable properties to produce robust multipurpose devices. Taking materials as an example, high-resolution and large-scale 3D printing makes it possible to further miniaturize and extend gear-based metamaterials." Fang Xin said.
Nature's review editor believes that such gear-based mechanical metamaterials are a viable way to make machine components tunable while maintaining structural strength and stability, such as by making the robot's structure softer or stiffer to better accommodate Actions like jumping and grabbing items.
Related paper information: https://doi.org/10.1038/s41563-022-01269-3
(Original title "A super "obedient" metamaterial was born from the inspiration of the internal structure design from the Taiji diagram")